The vacuum or modified atmosphere preservation and packaging technique is a staple for many industries. BMB of Molina di Malo (VI) has automated it, ingeniously innovating a consolidated technique.
BMB of Molina di Malo (VI) has developed a revolutionary and innovative technology for its vacuum or modified atmosphere packaging machinery. The new Conveyor MAP machine is able to operate in automatic mode, tripling the average vacuum packaging productivity.
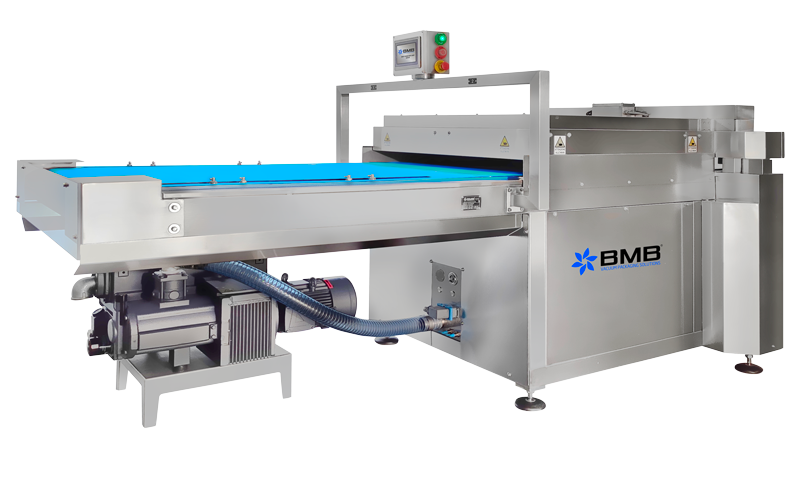
BMB has made the development and production of primary packaging machinery its focus. In particular, the company is focused on the production of vacuum and protective atmosphere packaging machines, thermosealers, thermoforming machines and shrink tunnels for the food, medical and industrial sectors.
Massimiliano Magnabosco, partner of BMB and head of research and development of the company, had been harboring the idea of automating the vacuum packaging process for some time. “The vacuum technique is consolidated for the maintenance of particular food, pharmaceutical, but also industrial products. The machinery created for this process has always been complex because the evacuation processes of the air and inert gas injection. Even with the advent of new techniques, the modified atmosphere had not at all simplified the process of the packaging machinery in envelopes which, however, remained manual or semi-automatic.”
Basically, to package a product in a vacuum or in a modified atmosphere, an operator who works on machinery that only manages stationary products is needed. The rhythm of packaging is therefore very far from the production rhythms that modern food and pharmaceutical production, for example, require or expect. Magnabosco has long studied for BMB an automated solution that would drastically reduce production times while guaranteeing absolute quality and safety of the processing.
Thus was born the first and only automatic belt vacuum packing machine which packs in maximum vacuum associated with a complete and effective protective atmosphere (MAP).
“In simple terms, we managed to make the product move and thus reduce the loading time. Our innovative packaging machine mounts nozzles, to be inserted into the packages to create the vacuum and to introduce the gas mixtures that prevent the proliferation of microbacteria, directly onto the conveyor belt. In this way it is the product that moves. Each machine can count 16 stations on a belt of about 2 meters, this means having 4 or 8 nozzles always ready for each loading station” explains Magnabosco.
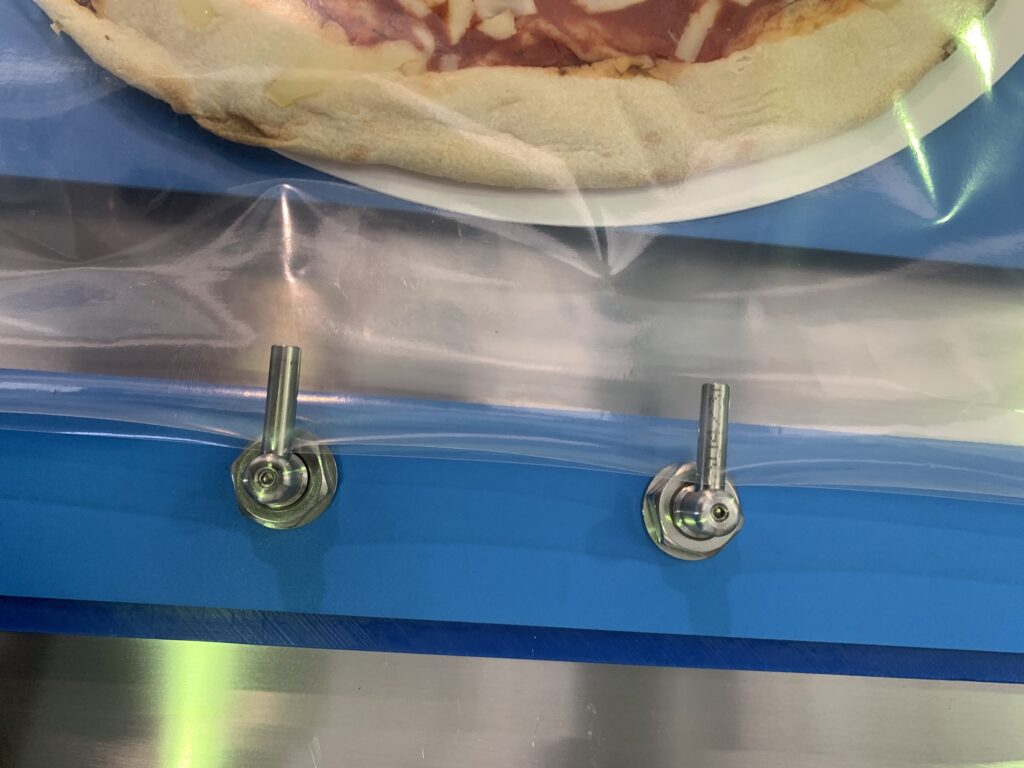
With the new BMB packaging machine, productivity is tripled by reducing the production cycle from about one minute to 20 seconds.
In this type of innovation, the belt and the drum motor which drives the movement of the product on the machine play a substantial role. Magnabosco has selected Interroll Italia for this innovative machine. Interroll supplies the DM0138 asynchronous drum motor covered in highly hygienic NBR rubber with IP69K protection degree. The coating of Interroll drum motors and conveyor belts lends itself particularly to the processes that BMB must carry out to position the nozzles and integrate other slots to obtain absolutely stable guides during movement. The exchange and dialogue between BMB and Interroll are constant also because the machines that BMB manufactures are customized for the specific final packaging.
The markets currently targeted by BMB are those of baked goods, fresh pasta, including filled pasta, wraps and pizzas and all those products that are packaged in ATM bags. In relation to the product and production, a plant is created which, therefore, is not standard, but is adapted to the customer’s needs.” This is possible thanks to the collaboration with Interroll Italia which supplies from time to time the motion components suitable for the supply.
“After two and a half years of studies and research, we are proud of the development of this new technological packaging application, ideal for baked goods and the pasta sector. We are already thinking about the dairy world for cheese and that of meat. We have not yet thought about the fish world, but we will also get to that as well as cooked and pre-cooked. We also do not exclude other industries that need special attention in packaging. The world of vacuum packaging is really evolving. We think only of the needs of the electronic component industry, rather than the pharmaceutical and medical ones” concludes Massimiliano Magnabosco.