DT heat-shrinking consists of immersing the packaged product in a tub containing hot water: once in contact with the heat source (hot water), the bag retracts adhering to the surface of the product and creating the effect called “Skin” (second skin).
The “immersion” system guarantees an excellent heat-shrinking result as the product is completely immersed and wrapped in water, an ideal situation for correct and complete heat transmission. There are two methods of water heating available: by electric resistances or by steam injection.
The temperature dispersion from the shrink chamber is very minimal as the chamber is closed and well isolated from the environment in which it is located. Each model is in fact equipped with an insulated tank, a stainless steel cover for closing the tank and a hood for the extraction of steam, to ensure maximum efficiency and low energy consumption.
The easy-to-use 7″ color touch-screen control panel allows you to store 20 work programs with the possibility of programming water pre-heating to save time at the start of the work shift, even remotely thanks to the interface Ethernet with Industry 4.0 technology.
The DT Line tunnels are ideal for in-line combination with BMB belt vacuum packaging machines and with automatic packaging lines.
The machine structure is completely in AISI 304 stainless steel and the electrical panel is in IP67 / NEMA 4 insulation class.
Specific use: For a wide variety of food products.
What types of bags? Only for shrink bags in different formats but in specific materials suitable for shrinking, easily manageable by adjusting the intensity of the water temperature as standard on each model.
Shrinking process steps with DT line tunnels
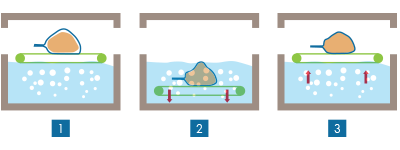
Technical Characteristics
Scheda Tecnica DT – 65
Structure | Stainless steel AISI 304 |
Control Panel | 7″ PLC Touch Screen |
Size (LxWxH) | 1500x1300x1755 mm |
Weight | 450 kg |
Useful dimensions (LxP – LxW) | 1210×660 mm |
Tank capacity | 350 l |
Useful tank depth | 280 mm |
Water heating | Electric resistors or Steam injection |
Electric consumption | 3KW (steam), 30/60KW (electric) |
Electric supply | 400V – 3PH + N + PE |
Pneumatic supply | 6/8 bar – dry and micro-filtered air |
Air consumption | 50 Nl/min |
Speed | Continuous cycle 0,6 m/sec |
Optional | Request information |
Scheda Tecnica DT – 85
Structure | Stainless steel AISI 304 |
Control Panel | 7″ PLC Touch Screen |
Size (LxWxH) | 1500x1500x1755 mm |
Weight | 550 kg |
Useful dimensions (LxP – LxW) | 1210×860 mm |
Tank capacity | 450 l |
Useful tank depth | 280 mm |
Water heating | Electric resistors or Steam injection |
Electric consumption | 3KW (steam), 36/42KW (electric) |
Electric supply | 400V – 3PH + N + PE |
Pneumatic supply | 6/8 bar – dry and micro-filtered air |
Air consumption | 50 Nl/min |
Speed | Continuous cycle 0,6 m/sec |
Optional | Request information |
Scheda Tecnica DT – 110
Structure | Stainless steel AISI 304 |
Control Panel | 7″ PLC Touch Screen |
Size (LxWxH) | 1500x1650x2100 mm |
Weight | 750 kg |
Useful dimensions (LxP – LxW) | 1210×1100 mm |
Tank capacity | 590 l |
Useful tank depth | 280 mm |
Water heating | Electric resistors or Steam injection |
Electric consumption | 3KW (steam), 42/50KW (electric) |
Electric supply | 400V – 3PH + N + PE |
Pneumatic supply | 6/8 bar – dry and micro-filtered air |
Air consumption | 50 Nl/min |
Speed | Continuous cycle 0,6 m/sec |
Optional | Request information |