Initial Situation
An Italian company specializing in 80cm cured-meat production relied on a manual system: each product was loaded into three double-chamber machines, then manually transferred to a metal detector for quality control. The process required numerous operators and slowed down the entire production flow, limiting the scalability and repeatability of packaging operations.
Challenge
- Increase production capacity: raise output from 12 packages/minute to higher rates to meet growing market demand.
- Seal reliability: ensure perfect vacuum sealing on every cycle, minimizing rejects.
- In-line inspection: integrate an automatic quality-control system, reducing human error to a minimum.
- Advanced automation: minimize manual interventions between the packaging machine and inspection systems.
Solution
We proposed the Conveyor Pro, an automatic vacuum-packaging machine with a conveyor belt and integrated inspection system, featuring:
- High-precision bi-active sealing bars for uniformly reliable seals
- Motorized feed belt with automatic speed adjustment according to the required throughput
- 7″ touch-screen panel for quick management of production batches
- Integrated inspection with synchronized metal detector, enabling automatic release or rejection of nonconforming products
- Automatic film cutting and package separation, eliminating manual handling along the line
Results
- Doubled throughput: 24 packages per minute, thanks to continuous flow and reduced dead times
- Consistent seal quality: zero rework due to seal failures, thanks to bi-active bars and precise control of pressure and temperature
- Minimal manual intervention: staff reassigned to supervisory roles, cutting direct labor costs by 50%
Conclusions
The Conveyor Pro enabled the customer to achieve a significant technological leap: faster, safer, and more controlled packaging with a high level of automation and consistent quality standards. This project demonstrates how integrating modern sealing
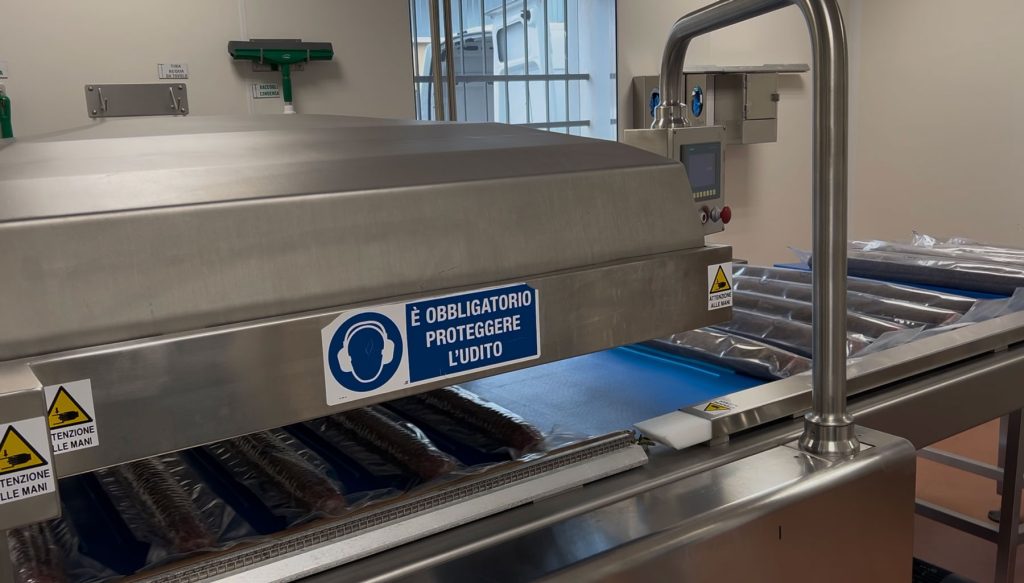